This is why you should digitise Maintenance Reports and service reports using digital forms and data capture apps
Forward-thinking organisations digitise maintenance reports due to the numerous benefits it offers, such as easy access to detailed information, informed decision-making capabilities that prevent equipment failure, and the convenience of having all necessary data at their fingertips. They also automate so many of the schedules you’re likely to forget about – keeping you legally compliant!
This step into the digital age allows maintenance teams to be more efficient and effective in their operations. If you’re out in the field, you can’t rely on paper, it’s time to step up with digital maintenance logs. We can help you do it with digital forms, but if you’re still on the fence as to whether the benefits of digital maintenance software can help you via a no-code app platform like forms2, read on.
Key Takeaways
Digitising maintenance reports brings improved efficiency, cost savings & increased sustainability – we know because our customers have experienced it first-hand. For instance, ArtSystems managed to save a whopping $40,000 by switching to forms2 digital forms and maintenance reports. This is a clear testament to the transformative power of going digital.
3 key industries benefit from digitisation with improved safety, visibility & decision making capabilities: facility managers, agriculture, and construction – If that’s YOU, you’ll LOVE this article.
Low code no-code data capture apps streamline data collection and provide predictive maintenance and automated alerts when its time to assess the health and quality of your assets.
The Power of Digital Maintenance Reports
By using a low code maintenance management system alongside digital forms, we can get a better handle on how our assets are performing and reduce maintenance costs, all while doing a little something good for the planet by reducing paper usage and waste.
For instance, consider the case where a crucial piece of machinery in a manufacturing plant breaks down unexpectedly. With a traditional system, this could lead to significant downtime and lost productivity.
However…
With a digital maintenance system using digital forms and data capture, we could have predicted this breakdown based on the machine’s performance data and scheduled maintenance before it became an issue.
The major benefit here is that we can predict maintenance schedules, set automated reminders, and prevent downtime. THAT’S the power of digital maintenance reports!
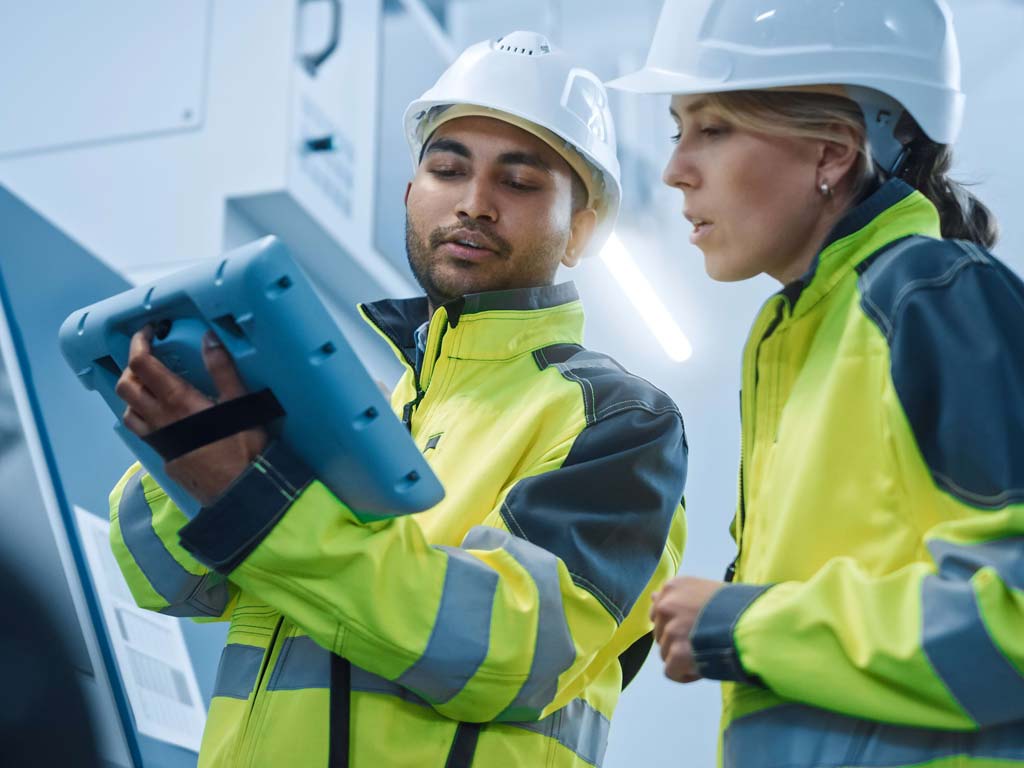
7 Key Benefits of Digitising Maintenance Reports
The benefits of digitising maintenance reports are industry agnostic – whether you’re in hospitality or retail. Here are seven solid reasons why going digital with your maintenance reports is a game-changer:
Faster Operations: Digital reports cut down on manual data entry, meaning your team can complete tasks quicker and move onto the next job. Plus, they’re accessible from any device, anywhere, which is a lifesaver if you’re managing multiple sites or working in the field. ArtSystems, for instance, saved a whopping $40,000 by switching to digital forms and apps. Their team could quickly access and update information, speeding up their operations.
Cost Savings: Digital reports eliminate the costs of paper, printing, and storage. They also reduce the time spent on data entry and retrieval, meaning your team can focus on more critical tasks.
Enhanced Legal Compliance: With digital reports, your compliance with health and safety laws is easier to manage and document. Your data, including safety inspections and incident reports, is securely stored in the cloud, safe from physical damage or loss. For example, in the construction industry, regular safety inspections are required by law. With digital reports, you can easily document these inspections, ensuring that you’re meeting your legal obligations and that sensitive information stays confidential. This is exactly what TD Construction Testing did to ensure they were complaint UKAS accreditation! Read the digital forms case study here
Sustainability: Digital reports mean less paper and less waste. It’s a small but significant step towards a greener operation. The European Camping Group slashed their paper use by 77% and saved an impressive $277,000 per year by going digital. That’s a huge win for both the environment and their budget.
Streamlined Procedures: Digital reports make it easy to track maintenance activities, identify trends, and optimize procedures. This leads to smoother operations, whether you’re managing a facility, a construction site, or a farm.
Better Communication: With digital reports, you can share updates instantly with your team, contractors, or clients. Everyone stays in the loop, reducing misunderstandings and delays.
Increased Decision-making Accuracy: Digital reports provide real-time, accurate data, enabling you to make informed decisions. You can spot issues before they become problems, plan preventative maintenance, and ensure your resources are used effectively.
In a nutshell, digitising your maintenance reports makes your job easier, your operations more efficient, and your life a whole lot less stressful.
Watch how our customer saved £30,000 Per year and sped up their reports by 90%.
7 Key Industries Benefiting from Digitising Maintenance Reports
A variety of industries can reap significant advantages from digitising their maintenance reports, as shown in a study conducted by forms2 on low code trends and statistics. Here’s a look at seven of these industries and how they can benefit:
Manufacturing: Digital reports in the manufacturing industry can streamline operations by providing real-time data on specific equipment such as conveyor belts, helping to prevent unexpected breakdowns and expensive repairs. They also facilitate inventory management of critical components, leading to significant cost savings.
Facility Management: With digitised reports, facility managers can better track maintenance activities of crucial infrastructure like HVAC systems, leading to improved efficiency and reduced costs. Automated reminders for regular inspections of safety equipment like fire alarms can also be set, ensuring no critical checks are missed.
Construction: Digital reports can help construction companies monitor the condition of their heavy machinery like excavators, anticipate potential issues, and schedule preventive maintenance, thereby minimising downtime and maximising productivity.
Agriculture: Farmers can use digital reports to track the maintenance of their machinery like tractors and irrigation systems, leading to improved efficiency, reduced costs, and increased crop yields.
Healthcare: Hospitals and other healthcare facilities can use digital reports to ensure their critical medical equipment like MRI machines are well-maintained and safe to use. This can help prevent equipment failures that could potentially impact patient care.
Transportation: Digital reports can help transportation companies monitor the condition of their vehicles like delivery trucks and schedule necessary maintenance, leading to improved safety, reduced costs, and increased efficiency.
Energy: Energy companies can use digital reports to track the maintenance of their critical infrastructure like wind turbines and power lines. This can help prevent unexpected breakdowns and ensure the reliable delivery of energy to customers.
In each of these industries, digitising maintenance reports not only improves efficiency and reduces costs but also contributes to sustainability by reducing paper waste.
Try the EASIEST digital form builder
14-day free trial
3 Essential Components to add to a digital Maintenance Report
Let’s talk about what a digital maintenance report should have to make your maintenance operations a breeze.
1. Asset Data
First off, you need to know what’s happening with your assets. That’s where asset data comes in. Think about a farmer’s tractor, for example. You’d want to know how many hours it’s been running, when it was last serviced, and if there have been any issues lately – maintenance software like this can help track that.
2. KPI’s
Next up are metrics or KPIs. These are like a report card for your operations. Let’s say you’re a facility manager or a landlord. You’d want to know how satisfied your tenants are, wouldn’t you? Well, customer satisfaction could be a KPI you’d track in your report.
3. Past Maintenance History
Lastly, you’d want a good overview of past maintenance efforts and a schedule for future ones. For example, if you’re in charge of a fleet of delivery vans, you’d want to know when each van was last serviced and when it’s due for the next check-up.
By putting all this info in one place, you can make smart decisions about what needs fixing or upgrading. Plus, it makes it a whole lot easier when it’s time to do a deep dive into how well your preventive measures are working.
And don’t forget about the added bonuses! For instance, if you’re in construction you could use image capture and signature capture to provide visual proof that a job has been completed. It’s all about making your maintenance operations smoother and more efficient, no matter what industry you’re in.
3 benefits of using low code data capture apps for Maintenance Reports
No-code data capture apps are your best friend when it comes to maintenance reports. They capture EVERYTHING and forget NOTHING. They’re so easy to use that anyone can build one, even if they’ve never coded a day in their life. You can customise your data capture apps to include any type of maintenance checks across any industry, whether you’re inspecting a tractor on a farm or a conveyor belt in a factory. And if you’re managing multiple locations, no problem!
You can set up your app to handle that too. Plus, these apps make it super easy to track task completion. Did Joe finish inspecting that HVAC system? Check the app! And the best part? All your maintenance reports can be stored in your tech stack, so you can access them anytime, anywhere. Now that’s what I call efficiency!
1. Making Data Collection a Breeze with Low Code Apps
Low code data capture apps are like the superheroes of data collection. They swoop in, streamline the process, cut down on errors and boost the quality of your data. Imagine Joe in construction, he can quickly and accurately gather information about his equipment, ensuring his maintenance reports are spot-on. This leads to smarter decisions and better management of his assets.
2. Easy Access and Teamwork for the Win
Maintenance software with low code data capture is like having a superpower. It gives your maintenance teams the ability to quickly access important information, work together more effectively, and stay updated with real-time insights. Sue in research can share her findings with her team instantly, keeping everyone in the loop and making their maintenance processes more efficient.
3. Predictive Maintenance
With no-code data capture apps, organizations can optimize asset performance and anticipate equipment failures. Steve, managing a vineyard with digital forms and data capture apps, can get early warnings about his wine press or irrigation system at risk for failure. He can then take preventive action, ensuring his vineyard operations run smoothly. These predictive maintenance applications support tailored learning algorithms and models, so Steve can create a unique strategy for managing his vineyard assets and preventing downtime. With this kind of tech, businesses are better equipped to handle unforeseen circumstances and keep an eye on equipment maintenance and operational improvements.
Top Tips for Digital Maintenance Reporting
To ride the wave of successful asset management, you gotta focus on quality data collection, regular reporting, and always be ready for a tune-up. Let’s see how we can turn the benefits of digital maintenance reports up to eleven:
Nail that Quality Data Collection
Quality data collection is the secret sauce for successful maintenance reporting. You gotta make sure your data is as accurate and consistent as a Swiss watch. How do you do that? By using top-notch tools like low code no code app builder platform forms2. It helps you collect information, reduce errors, and maintain the integrity of your records. So, you can sit back and relax knowing your decisions are based on the latest and greatest details.
Regular Reporting and Review
Think of regular reporting and review as your trusty sidekicks in managing assets, improving preventive maintenance operations, and optimising your maintenance processes. These reports are like a crystal ball, helping you make data-driven decisions, spot trends, and identify areas that need a little TLC. Regular check-ins keep your routine activities proactive and costs under control, including those pesky corrective ones. And reviewing the records? It’s like having a personal finance guru, giving you insights into your spending on labour or materials.
Continuous Improvement
Maintenance teams and managers should always be tracking data. By analysing the data you’ve collected, you can pinpoint areas where you can make improvements or act on potential problems. This way, your maintenance operations stay relevant and in line with industry standards. Regular evaluation and planning help you stay sustainable and make sure there are no machinery breakdowns, or unwanted leaks in a vineyard irrigation system because you forgot to service it!
It’s easier than you think to switch to digital maintenance forms & apps
Look, dealing with assets and dodging equipment failures doesn’t have to be a headache. Digital maintenance reports are here to make your life easier. They’re like your personal assistant, streamlining your operations and helping you save money. And the best part? It’s not rocket science. With the help of low code no code data capture applications, you can maximize your assets’ performance and make your operations more sustainable. So, why not give it a shot with forms2 and start to digitise maintenance reports and service reports today?
This is how fast you can create a digital form…it takes LESS than 60 seconds.
Try the EASIEST digital form builder
14-day free trial
Frequently Asked Questions
What is a maintenance service report?
Maintenance Service Report is a report which provides all the details of services done to certain vehicles, machinery or equipment. This document serves as proof that proper care and maintenance was given so there would be no need for repeat requests.
How do you write a good maintenance report?
A maintenance service report should encompass key elements to help with maintenance and reliability functions and upkeep planning. These include the categories, site, date/time of inspection, a description along with images taken during said evaluation as well as an authentic signature concluding the document. Keeping in mind that its format is casual yet informative. Make it easy to understand so that clients and team members can easily interpret action points.
What are the 4 types of system maintenance?
Maintaining a system correctly requires the implementation of four distinct types corrective maintenance – preventive, corrective, adaptive and perfective maintenance. These all help to keep the system up-to-date and running as it should be.
What are the benefits of a digital maintenance report?
A digital maintenance report is essential to improving productivity and maximising profits. It helps with organising the upkeep of machinery, ensuring all tasks are carried out as scheduled, automating maintenance schedules and reducing manual tracking, so that operations run efficiently and you don’t have to worry about maintenance planning.
What is digital maintenance planning?
Digital maintenance planning is the use of modern technology, including low code data capture apps and digital forms, in combination with traditional maintenance activities, to provide real-time data and streamline these processes. This type of advanced maintenance aims at increasing accuracy and productivity within routine maintenance tasks. The use of low code no code data capture apps allows for simplified data accumulation and improved accessibility, making the process even more efficient.